Great Info About What Is The Difference Between MRP And DRP
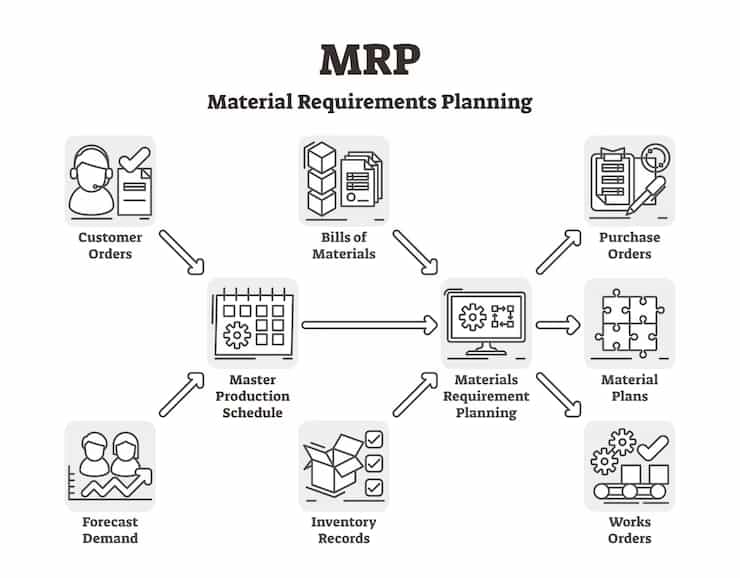
Mengenal Material Requirements Planning (MRP) & Fungsinya
MRP vs. DRP
1. Understanding the Basics
Ever felt like you're swimming in a sea of acronyms when trying to manage inventory and production? You're not alone! Two biggies that often get tossed around are MRP and DRP. Think of them as siblings in the supply chain family, related but with different jobs. MRP, or Material Requirements Planning, is the older sibling, focused on manufacturing. DRP, or Distribution Requirements Planning, is the younger, more outward-looking sibling, concerned with getting products to where they need to be in the distribution network.
The core idea behind both is simple: ensure you have the right stuff, in the right quantity, at the right time. But the "where" and "why" behind those requirements differ. MRP lives inside the factory walls, figuring out what raw materials and components are needed to build the finished goods. DRP, on the other hand, operates across warehouses and distribution centers, planning the flow of finished products to meet customer demand. Imagine MRP as the chef planning the ingredients for a specific dish, and DRP as the delivery service ensuring that delicious dish arrives at your doorstep piping hot!
So, if you're a manufacturing plant trying to figure out how many widgets you need to order to make your whiz-bang gizmos, MRP is your friend. If you're a distributor trying to decide how many whiz-bang gizmos to ship to your regional warehouses to satisfy customer orders, DRP is the tool you reach for. It's all about context!
Often, companies use these systems together, creating a synchronized planning process. MRP feeds into DRP. What the factory plans to produce, drives the distribution plan. Its about aligning internal production with external demand signals. If you want a successful supply chain, its critical that the two areas work in unison.
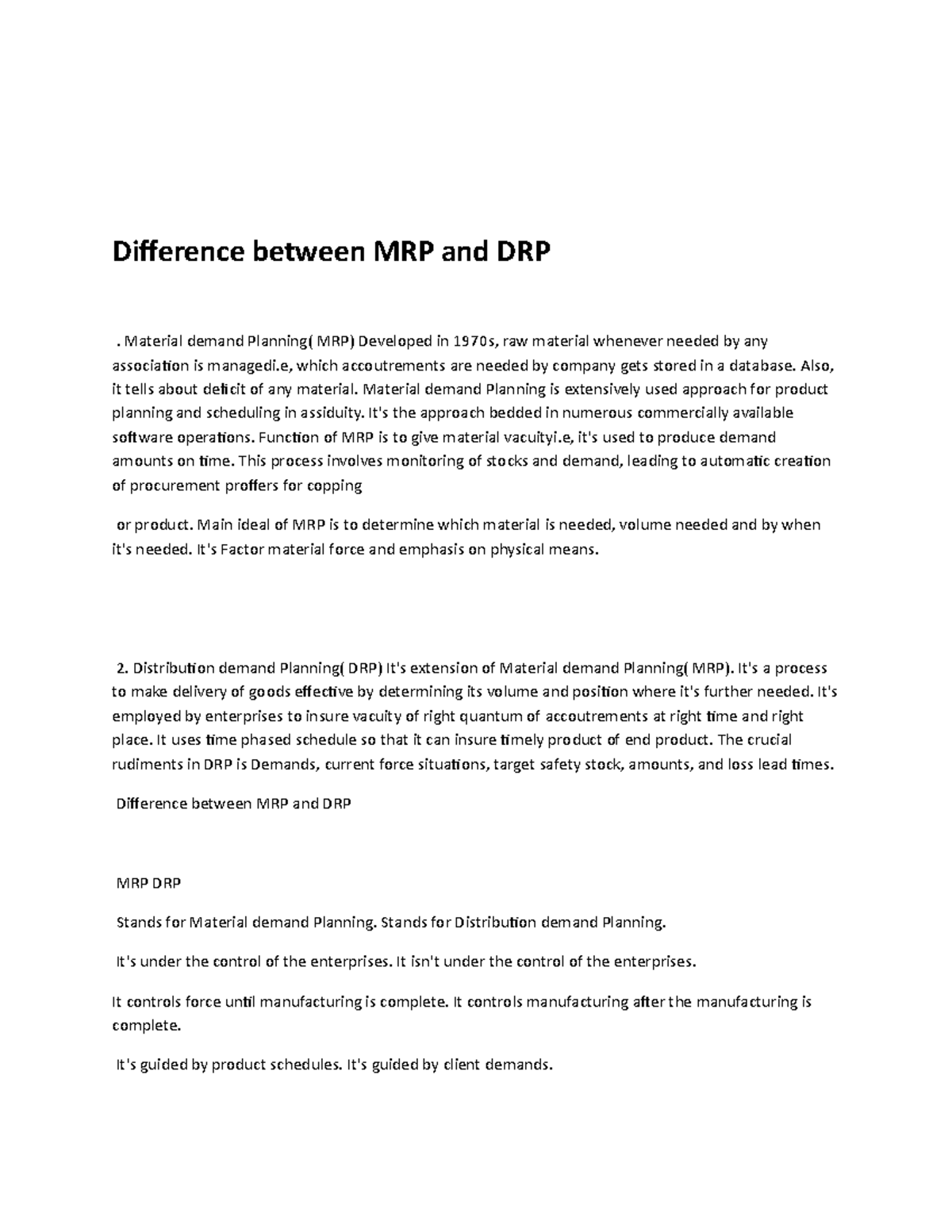
Decoding Material Requirements Planning (MRP)
2. Peering Inside the Factory Walls
Let's zoom in on MRP. It's like the command center for manufacturing operations. At its heart, MRP uses a bill of materials (BOM), which is essentially a recipe that lists all the ingredients (raw materials, components) needed to make a product. It also considers existing inventory levels and scheduled production. Armed with this information, MRP calculates what needs to be ordered and when to meet the production schedule.
Think of it like this: you're planning a pizza party. Your BOM is the pizza recipe (dough, sauce, cheese, toppings). MRP checks your pantry to see what you already have. It then calculates how much more of each ingredient you need to buy, and when you need to buy it, so you can make all those pizzas on time. It considers lead times for ordering ingredients.
MRP is usually used to plan production, purchasing, and inventory control. It can help companies reduce inventory levels, improve production efficiency, and meet customer demand on time. All worthy goals, right? By optimizing your inventory, you can reduce waste and reduce storage expenses. The advantages of using MRP far outweigh the resources needed to implement it.
However, MRP isn't a crystal ball. It relies on accurate data — that BOM needs to be spot-on, and inventory records need to be up-to-date. Garbage in, garbage out, as they say! If the data is poor, the plan will not function properly. It can also struggle with unexpected disruptions, like a sudden surge in demand or a supplier issue.
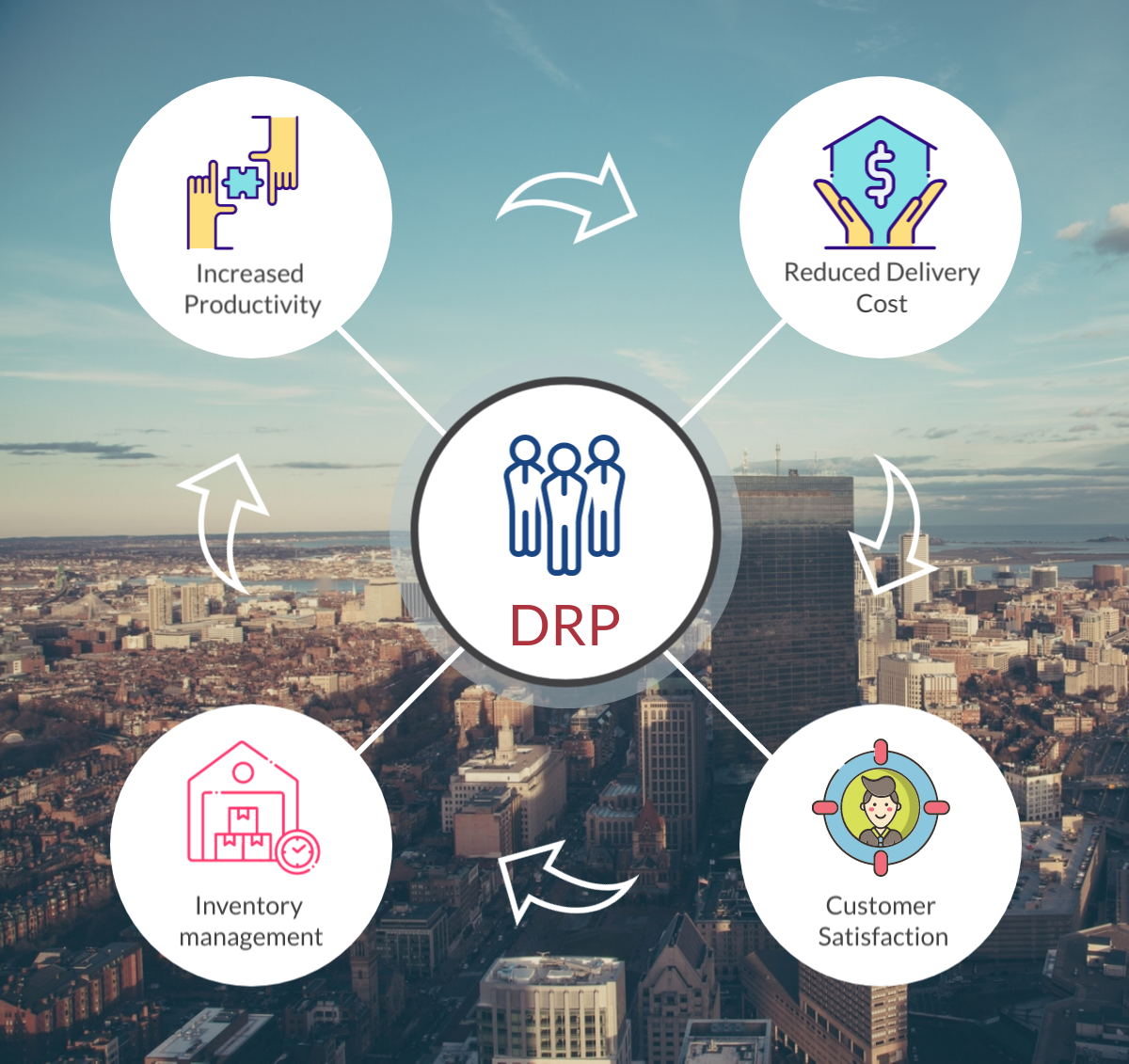
Understanding The Distribution Requirements Plan (DRP)
Delving into Distribution Requirements Planning (DRP)
3. Extending Your Reach to the Customer
Now, let's shift gears and explore DRP. While MRP focuses on internal manufacturing needs, DRP looks outward to the distribution network. DRP helps you plan the distribution of finished goods across multiple locations, such as warehouses, distribution centers, and retail stores. It predicts customer demand in different locations. It calculates how much inventory each location needs to meet that demand. With this information, DRP creates a distribution plan that specifies how much of each product should be shipped from each location to each other location.
Imagine you are selling t-shirts. You have a warehouse in New York and a warehouse in Los Angeles. DRP helps you decide how many t-shirts to stock in each warehouse, and when to ship them from one warehouse to the other, based on predicted demand in each region. It helps to keep your customers happy.
The benefits of DRP are similar to those of MRP: reduced inventory levels, improved customer service, and optimized distribution costs. By having the right products in the right places at the right time, you can satisfy customer demand more effectively and avoid stockouts or overstocking. Having the right amount of product on hand means that you can lower transportation costs.
DRP, like MRP, depends on accurate data. This includes forecasts of customer demand, lead times for shipping products between locations, and inventory levels at each location. In a volatile market, forecasting can be difficult. Good software can help to minimize the margin of error. DRP can also be impacted by disruptions, such as transportation delays or unexpected surges in demand in a specific region.
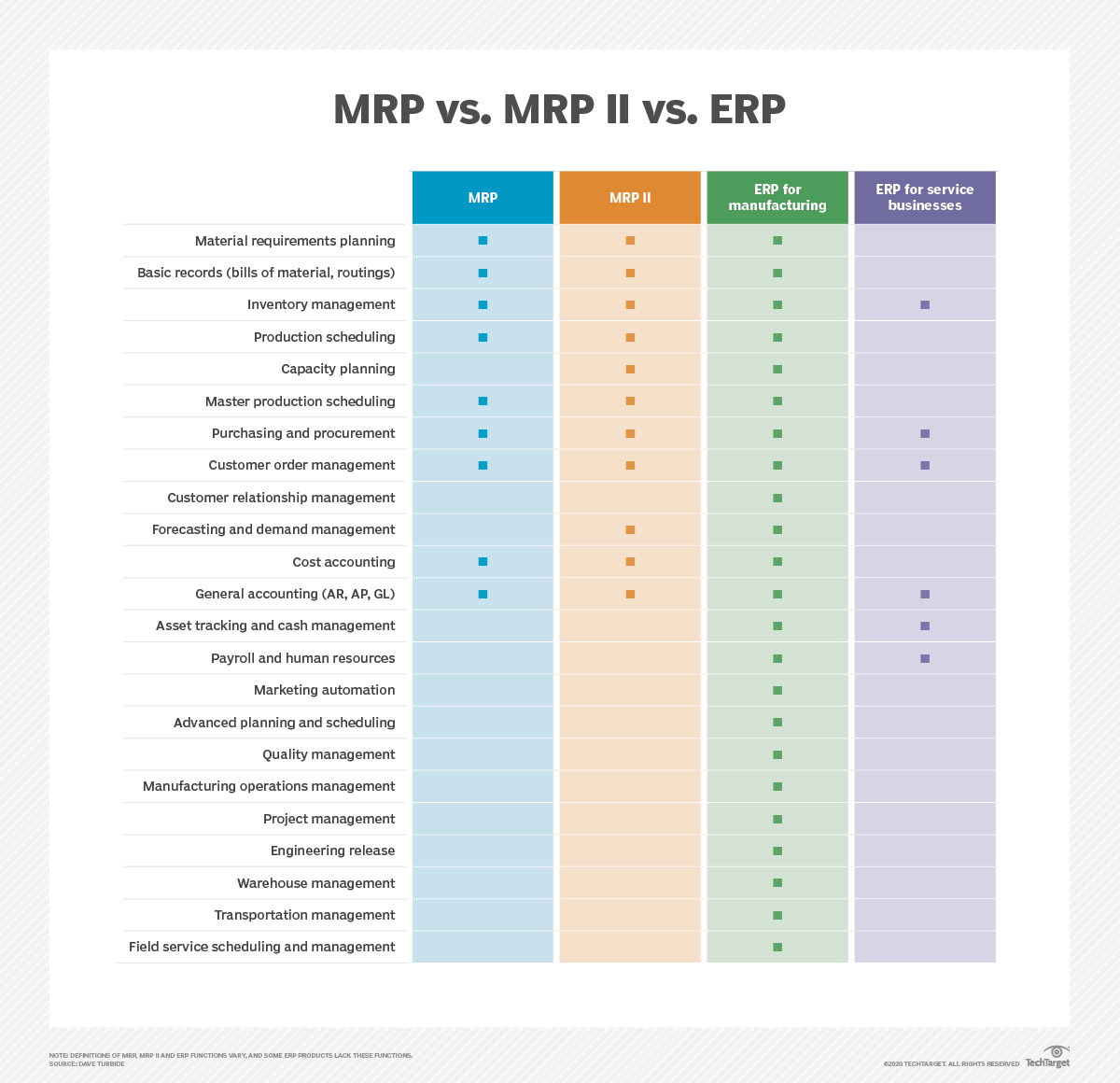
What Is Material Requirements Planning (MRP)?
Key Differences Summarized
4. Side-by-Side Comparison
Let's boil it down to the key differences: Think of MRP is focused primarily on the components necessary to create a product. It ensures that all of the parts are available when they are needed. DRP, is focused on the distribution channel, that are the goods available when the customers want to buy it.
Data Focus: MRP relies heavily on the bill of materials, inventory levels, and production schedules. DRP emphasizes customer demand forecasts, distribution lead times, and inventory levels at each distribution location.
Perspective: MRP takes an inside-out approach, starting with internal manufacturing needs. DRP takes an outside-in approach, starting with external customer demand.
In essence, MRP is about making sure you can make the product, while DRP is about making sure you can deliver the product. Both are vital for a smooth-running supply chain.
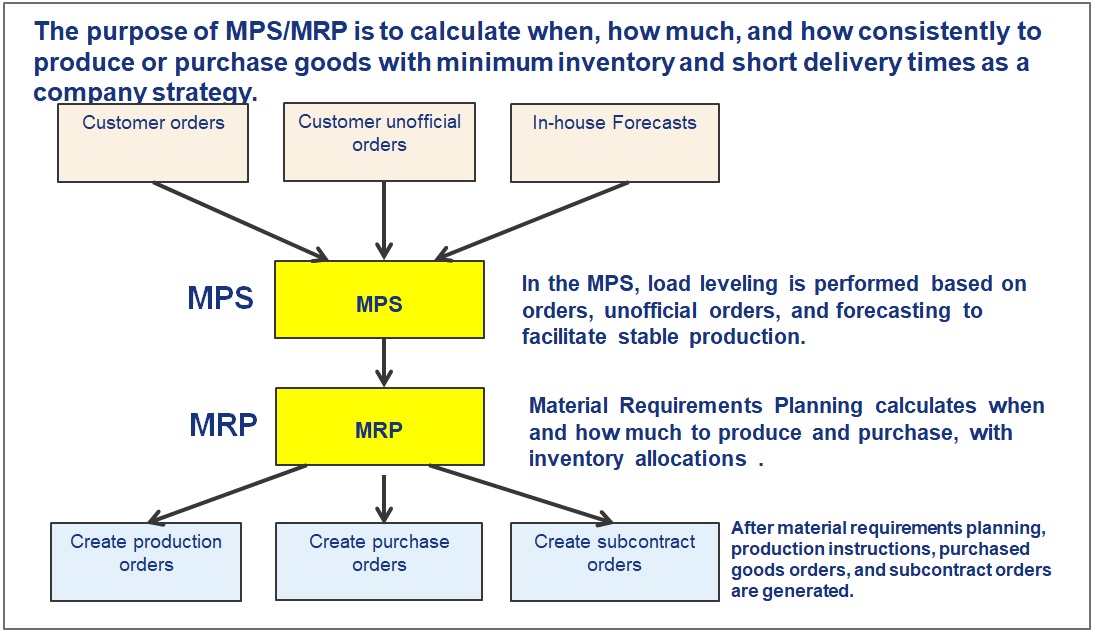
Master Production Schedule(MPS) And Material Requirements Plan(MRP
Combining MRP and DRP for Supply Chain Harmony
5. The Power of Integration
The real magic happens when MRP and DRP work together seamlessly. By integrating these two systems, you can create a closed-loop planning process that aligns production with distribution and ensures that products are available to meet customer demand, efficiently and cost-effectively. Think of it as a well-choreographed dance between manufacturing and distribution, where each step is perfectly synchronized.
Integrated MRP and DRP systems can also provide better visibility across the entire supply chain, allowing you to identify potential problems and take corrective action quickly. For example, if DRP detects a sudden increase in demand for a particular product in a certain region, it can signal MRP to increase production of that product. Or, if MRP anticipates a production delay, it can inform DRP to adjust distribution plans accordingly.
This collaboration can significantly improve customer service levels, reducing the likelihood of stockouts or late deliveries. Ultimately, it boosts efficiency, reduces costs, and enhances your overall supply chain performance.
Todays sophisticated supply chain management software often includes integrated MRP and DRP modules. The software will help in tracking raw material orders and shipment dates. Many of these software packages also include real time inventory tracking so you can make timely adjustments as needed.
Differences Between MRP And DRP Planning Systems PDF
Frequently Asked Questions (FAQs)
6. Answering Common Questions
Q: Can a small business benefit from MRP or DRP?A: Absolutely! While these systems are often associated with larger companies, even small businesses can benefit from implementing MRP or DRP, especially if they have complex manufacturing processes or distribution networks. Start with a simple solution and scale up as needed.
Q: Are MRP and DRP software expensive?A: The cost of MRP and DRP software varies widely depending on the features, complexity, and vendor. There are options available for different budgets, including cloud-based solutions that offer pay-as-you-go pricing. Do your research and compare different options to find the best fit for your needs.
Q: What happens if my demand forecast is wrong in DRP?A: If your demand forecast is inaccurate, DRP might recommend stocking too much or too little inventory in certain locations. Regular review and adjustment of your forecast are key. Modern DRP systems often incorporate sophisticated forecasting techniques, including machine learning, to improve accuracy.