Out Of This World Tips About What Is The Best Alternative For Soldering Wire

What To Do When Your Solder's Gone AWOL
1. Exploring Wire Connection Options
Okay, so you're in the middle of a project, maybe wiring up a sweet new LED setup for your bike or fixing that perpetually broken lamp, and BAM! You realize you're out of solder. Or worse, your soldering iron decided to take an unscheduled vacation (aka, it's broken). Don't panic! Soldering, while a fantastic method, isn't the only way to join wires. Let's dive into some alternative solutions that can save the day — or at least get you back to your project sooner rather than later.
The main point here is finding a secure and reliable connection. A wobbly, poorly connected wire can lead to all sorts of problems, from intermittent outages to, in extreme cases, fire hazards. So, we're not just looking for a quick fix; we're looking for a good fix that will stand the test of time (or at least until you can get your hands on some more solder!).
Consider your project's requirements when selecting an alternative. Is it a low-voltage circuit that won't experience much strain? Or is it something more demanding, like wiring up a car stereo? The answer will steer you toward the most appropriate alternative. Plus, think about whether this is a temporary solution or if you're aiming for something more permanent.
Let's face it, sometimes you just need to get the job done now. Maybe you're on a remote camping trip and your trusty flashlight konked out. Or perhaps you're dealing with a critical repair in your home and can't wait for a supply run. Whatever the reason, having a few alternative wire-joining tricks up your sleeve can be a lifesaver. The goal is safe and functional.
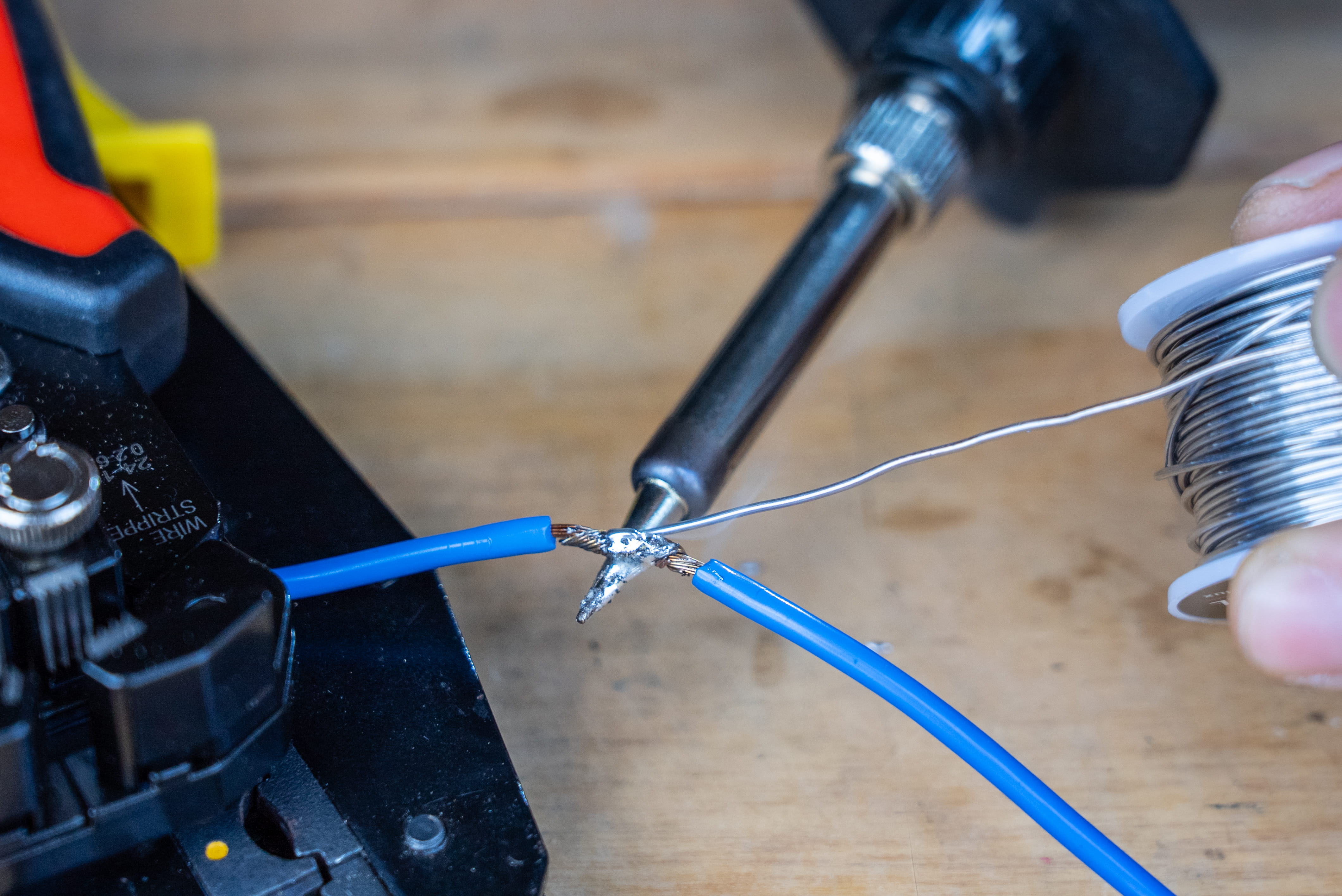
Twist and Shout (But Securely!)
2. The Connectorized Solution
Probably the most popular and reliable alternatives to soldering are wire connectors, and there's a whole universe of them out there. We're talking about everything from simple twist-on connectors (those little colored caps you see everywhere) to more sophisticated lever-lock connectors. They're designed to create a secure, insulated connection without needing heat.
Twist-on connectors, often called wire nuts, are super easy to use. You strip the wires, twist them together (usually clockwise), and then screw the connector onto the twisted ends. Make sure the wires are twisted tightly together before applying the connector. This helps ensure a good electrical connection and prevents them from slipping out later. Don't just rely on the connector to do all the twisting!
Lever-lock connectors are a bit more advanced and, in my opinion, provide a more reliable connection. You simply strip the wires, insert them into the connector, and then flip the lever to lock them in place. These are great because they provide a consistent clamping force and are less prone to loosening over time. They're also reusable, which is a nice bonus.
The beauty of wire connectors is their simplicity and reusability. Need to change something later? Just unscrew the connector or release the lever, and you're good to go. This makes them ideal for projects where you might need to make changes or adjustments down the line. Plus, they offer a degree of insulation, protecting the connection from shorts and accidental contact.
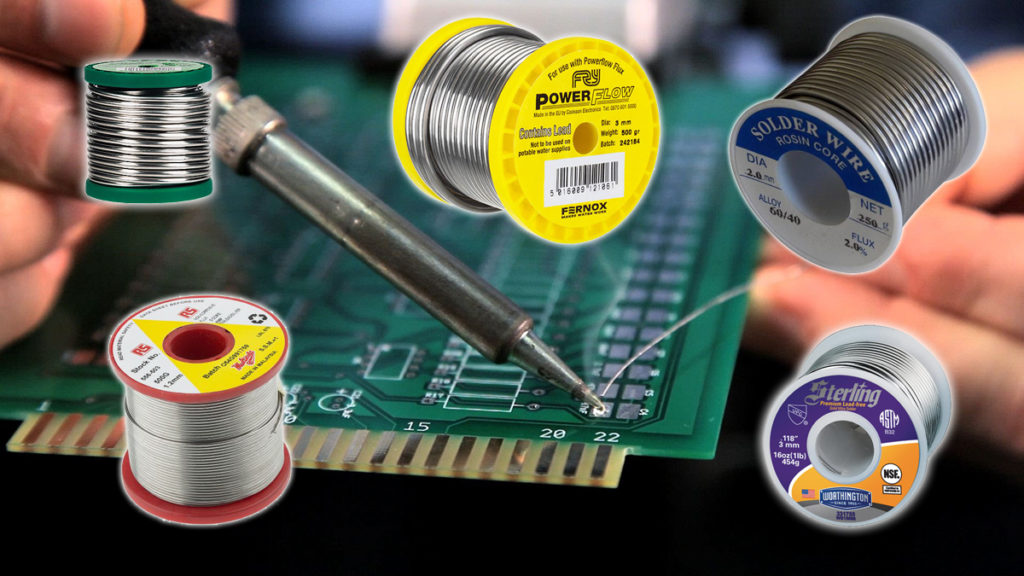
Why I Solder Copper Wires DIY Alternative Energy From Home
Crimping
3. The Crimp Connection Method
Crimping is another excellent method for joining wires without soldering. It involves using a specialized tool — a crimper — to mechanically compress a connector onto the wires. This creates a strong, gas-tight connection that's resistant to vibration and corrosion.
There's a wide variety of crimp connectors available, from butt connectors for joining two wires end-to-end to ring and spade terminals for connecting wires to screws or bolts. The key is to choose the right connector for your specific application and wire gauge. Using the wrong size connector can result in a weak or unreliable connection. The right size is the key for this method to be secure.
The crimping process is pretty straightforward. You strip the wires, insert them into the connector, and then use the crimper to compress the connector around the wires. It's important to use the correct crimping tool and to apply the proper amount of force. Too little force, and the connection will be weak. Too much force, and you could damage the connector or the wires. Practice makes perfect here!
Crimped connections are generally very reliable and are often used in automotive and industrial applications where vibration and harsh environments are common. They're also a good choice for permanent connections, as they're less likely to loosen or corrode over time. The best crimpers have a ratcheting mechanism to ensure a consistent crimp every time. Look for those, if you can!

How To Solder Wire StepbyStep Process
The Old-School Twist and Tape (Use With Caution!)
4. The Temporary Fix Approach
Okay, let's be honest. We've all been there. Desperate times call for desperate measures. And sometimes, that means resorting to the classic twist and tape method. This involves stripping the wires, twisting them together, and then wrapping the connection with electrical tape.
Now, I'm going to be upfront: this is not the ideal solution. It's really more of a temporary fix than a permanent one. The problem is that the connection can loosen over time, and the electrical tape can dry out and become brittle. This can lead to a poor connection, which can cause all sorts of problems.
However, if you're in a pinch and need to get something working quickly, twist and tape can be a viable option — as long as you do it correctly. Make sure the wires are twisted together very tightly, and use high-quality electrical tape. Wrap the tape tightly and thoroughly, overlapping each layer to create a good seal.
If you do use twist and tape, be sure to monitor the connection regularly and replace the tape if it starts to deteriorate. And, of course, plan to replace it with a more permanent solution as soon as possible. Think of it as a Band-Aid, not a permanent solution. It'll get you by, but you wouldn't want to run a marathon with just a Band-Aid, right?
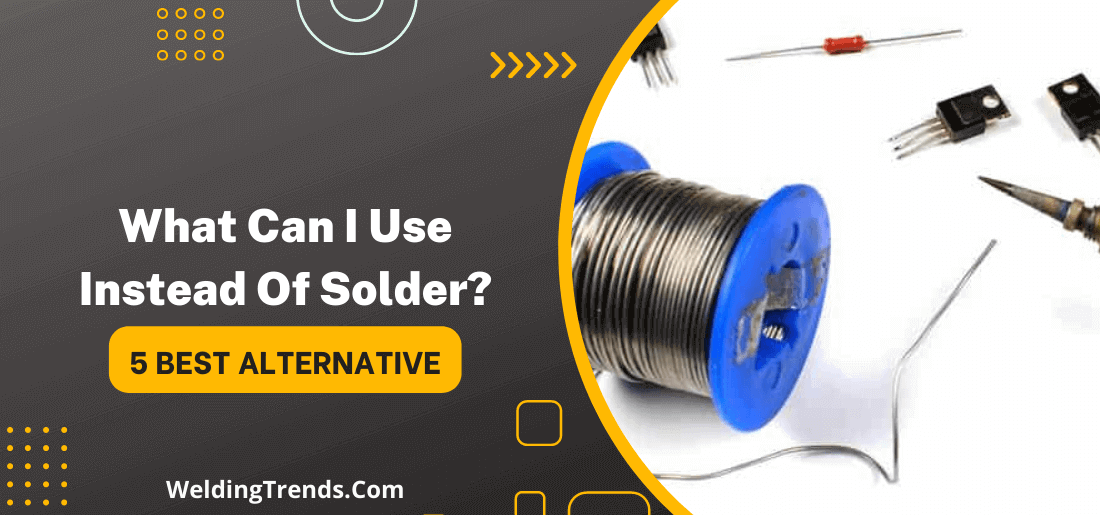
What Can I Use Instead Of Solder?
Cold Welding
5. Pressure Connection Technique
Cold welding, or pressure welding, is a fascinating technique that joins wires (typically softer metals like copper or aluminum) by applying high pressure. This forces the atoms of the two wires to intermingle, creating a bond without the need for heat or any filler material. It's like they're becoming one — really friendly atoms!
While it sounds like something out of a science fiction movie, cold welding is actually a well-established process used in various industries. However, it's not as commonly used for basic wire connections because it typically requires specialized equipment. You're not likely to find a cold welding tool at your local hardware store.
The quality of a cold-welded connection is highly dependent on the pressure applied, the cleanliness of the surfaces, and the materials being joined. If done correctly, it can create a very strong and reliable bond that's resistant to corrosion and vibration. However, if the pressure is insufficient or the surfaces are contaminated, the connection will be weak and prone to failure.
While it may not be the most practical alternative for most DIYers, cold welding is an interesting option to be aware of. As technology advances, we may see more affordable and accessible cold welding tools become available for everyday use. Imagine a future where you can simply press two wires together and they're instantly joined! The future is here!

Alternatives To Soldering Everything You Should Know NerdyTechy
FAQ
6. Your Burning Wire Questions Answered
Still got questions about alternatives to soldering? Let's tackle some of the most common inquiries:
Q: Are solderless connectors as reliable as soldering?A: In many cases, yes! High-quality crimp connectors and lever-lock wire connectors can provide very reliable connections, especially when properly installed. However, soldering is often preferred in high-vibration or high-stress environments.
Q: Can I use electrical tape as a permanent solution for joining wires?A: Nope! Electrical tape is really only meant as a temporary solution. Over time, the adhesive can dry out, causing the tape to unravel and exposing the connection. This can lead to shorts, fires, and general electrical mayhem. Use a proper connector for long-term reliability.
Q: What's the best type of wire connector to use?A: It depends on the application! For general-purpose connections, twist-on connectors or lever-lock connectors are a good choice. For more demanding applications, crimp connectors are often preferred. Consider the wire gauge, the environment, and the expected lifespan of the connection when making your decision.